De acordo com The Nature of Fashion, um relatório de 2021 publicado pelo Biomimicry Institute, mais de 60% das fibras têxteis são sintéticas derivadas de produtos petroquímicos. As fibras petroquímicas, sejam feitas de matérias-primas recicladas ou virgens, não são biodegradáveis. Além disso, os processos usados para fazer essas fibras liberam produtos químicos de gases de efeito estufa (GEE) e outros resíduos, que se acumulam em nosso solo, ar e água no final da vida útil.
Dado o apetite global por fast fashion e outros produtos têxteis, eles só vão aumentar. A solução pode estar em uma nova geração de polímeros e fibras biossintéticos. Feito pelo homem a partir de materiais de base biológica – incluindo resíduos de alimentos, algas, óleo de mamona ou tecidos de algodão reciclado – as fibras biossintéticas podem ser projetadas para substituir o poliéster e nylon tradicionais.
Embora nem todas as fibras sintéticas de base biológica sejam biodegradáveis, elas permitem que os combustíveis fósseis virgens permaneçam no solo.
Fibras com menos emissões
As fibras sintéticas, sejam elas petroquímicas ou de base biológica, são compostas por certos monômeros derivados de matérias-primas. A utilização de materiais de base biológica para criar os monômeros usados para fabricar fibras sintéticas resulta em menos emissões de GEE.
Avantium NV, uma empresa de tecnologia especializada em química renovável, lançou recentemente uma avaliação do ciclo de vida (LCA) de sua plantMEG (monoetilenoglicol), derivada do açúcar de beterraba via Ray Technology da Avantium.
O MEG é um dos principais blocos de construção do poliéster e geralmente é baseado em insumos de combustíveis fósseis. A avaliação do ciclo de vida (LCA) plantMEG da Avantium mostra uma redução de emissão de GEE de até 83%, em comparação com o MEG baseado em fósseis.
Apresentando o succinato de polibutileno
A empresa Kintra Fibers descreve sua receita proprietária para a criação de PBS como um processo “da fazenda à fibra”. O succinato de polibutileno (PBS) é um poliéster, como o PET, exceto que os respectivos monômeros usados para fazer o PBS são o resultado da fermentação usando açúcares derivados de trigo, milho e similares. A Kintra integra a sua tecnologia de materiais na cadeia de valor da moda ao nível da resina e do fio.
“Precisamos de mais independência de matéria-prima, mas é um investimento enorme”, diz o cofundador e CEO da Kintra, Billy McCall. O PBS da Kintra foi projetado para substituir o poliéster. De acordo com McCall, a fibra parece caxemira, mas exibe pontos fortes semelhantes ao PET ou nylon, tornando-a apropriada para o luxo dos mercados ativo/externo.
A resina Kintra pode ser fiada no mesmo equipamento usado para fazer fio PET e tolera bem o processamento em alta temperatura. Mais importante, o PBS da Kintra é compostável. Ele tinge a temperaturas de 70 – 80˚ C, economizando energia em comparação com o tingimento tradicional de poliéster.
A Kintra está em transição para o estágio de amostra de fios e tecidos, com planos de fazer um teste de vestuário com o grande investidor Pangaia. “Até agora é um passo de cada vez, mas com o tempo descobriremos ainda mais aplicações para a fibra”, explica McCall.
“Precisamos de uma escala significativa para fazer um LCA completo, mas estamos começando a juntar algumas partes individualmente. Queremos criar um material que seja útil como vestuário, mas que não crie poluição plástica persistente enquanto você o usa ou quando se livra dele.”
Um celulósico revolucionário
A inovadora têxtil suíça HeiQ lançou recentemente o AeoniQ, um fio de celulose de filamento contínuo baseado em uma nova fibra derivada de materiais “negativos em carbono”. Criado a partir de polímeros de terceira geração a partir de matérias-primas celulósicas, incluindo algas, cana-de-açúcar, palha e cânhamo, que capturam carbono durante seus ciclos de crescimento. O AeoniQ foi projetado para ter um desempenho comparável ao poliéster, nylon e celulose regenerada.
A HeiQ chama o novo fio de “um divisor de águas para toda a indústria têxtil”, pois foi projetado para ser reciclado repetidamente sem comprometer a qualidade. A empresa está construindo uma planta de produção piloto para AeoniQ na Áustria, capaz de fornecer uma capacidade anual de 100 toneladas a partir do segundo trimestre de 2022, com planos para uma planta em grande escala e remessas comerciais até o primeiro trimestre de 2025.
Enrique Herrero Acero, diretor de tecnologia da HeiQ AeoniQ, diz: “Em relação aos testes têxteis, era obviamente essencial que pudéssemos demonstrar o potencial do fio com têxteis reais e dentro do escopo de nossas possibilidades. A produção têxtil em pequena escala já foi experimentada e testada com sucesso.” A LYCRA Company já está a bordo como parceira investidora, e a marca de vestuário premium Hugo Boss acaba de anunciar seu primeiro investimento vinculado à sustentabilidade com a HeiQ AeoniQ LLC.
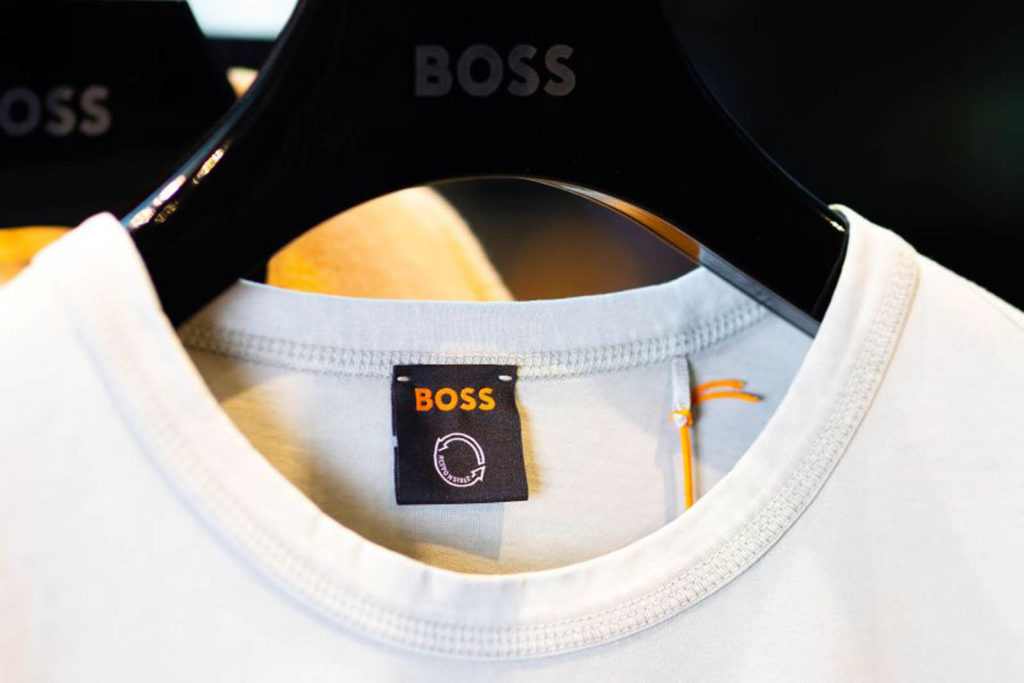
Fibras de filamentos giratórios de celulose
Pesquisadores do Instituto Alemão de Tecnologia Têxtil e Engenharia de Processos em Denkendorf (DITF) desenvolveram uma tecnologia chamada HighPerCell (HPC) baseada no uso de líquidos iônicos (basicamente um sal em estado líquido) para produzir fibras de filamento contínuo de celulose.
O processo é uma alternativa ecológica ao processo de viscose amplamente utilizado. Os líquidos iônicos não são tóxicos nem inflamáveis, e são fáceis e quase completamente recicláveis após o processo de fiação. Fiadas a partir de matérias-primas de celulose, como polpa de madeira, cânhamo e quitina (comumente derivadas de células de camarão), as fibras de HPC são caracterizadas por alta resistência e são apropriadas para aplicações técnicas.
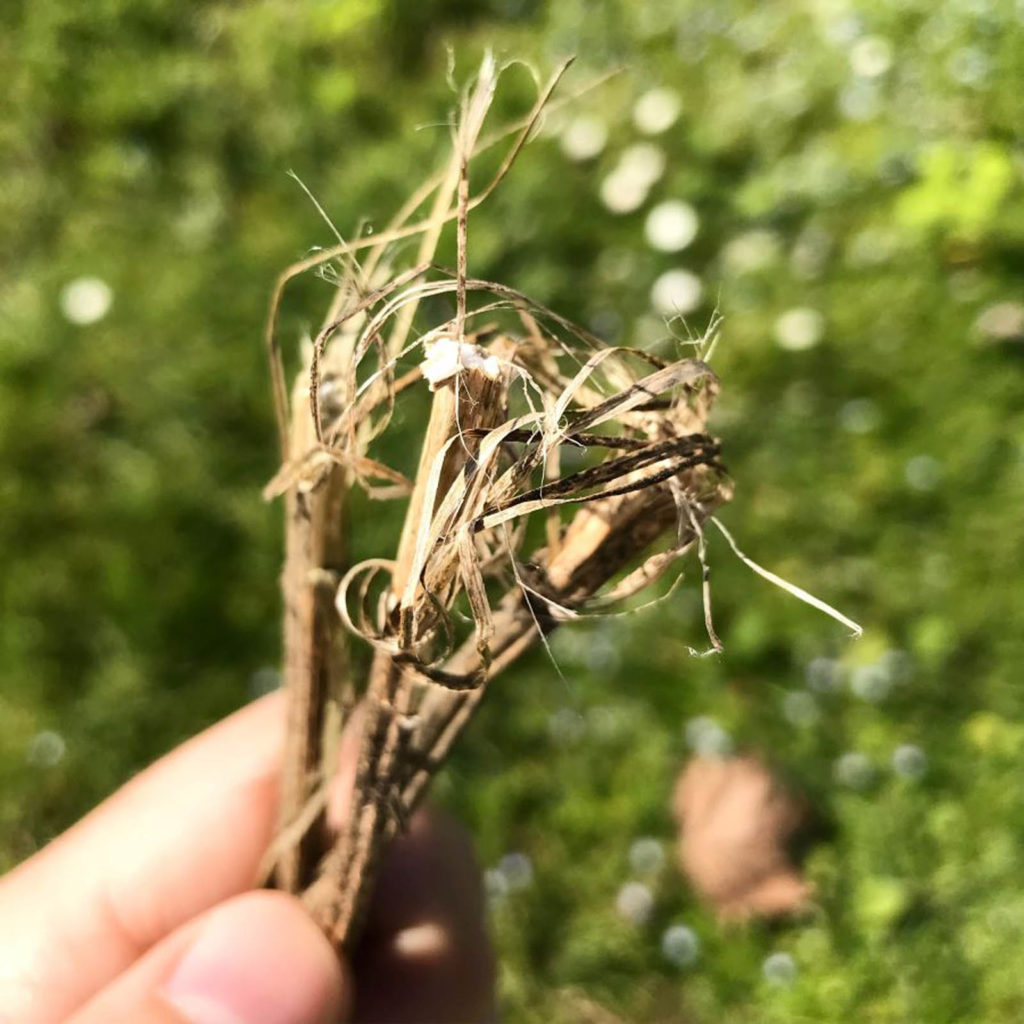
“Podemos imaginar que os filamentos podem ser usados em múltiplas aplicações: têxteis (vestuário e técnico) e materiais de reforço (HPC e HPCCarbon); em princípio, em todos os lugares, viscose e liocel são usados; e como substituto de poliéster ou algodão em certas aplicações”, diz o Dr. Antje Ota, vice-chefe do centro de competência, materiais biopoliméricos da DITF.
Os produtos feitos de fibras de HPC são recicláveis e biodegradáveis, acrescenta Ota. Vestuário e resíduos de tecidos de algodão ou celulose regenerada em fim de vida também podem ser reciclados pela tecnologia HPC. A DITF iniciou recentemente uma colaboração com a recém-fundada Technikum Laubholz para a produção piloto de fibras HPC e HPCCarbon.
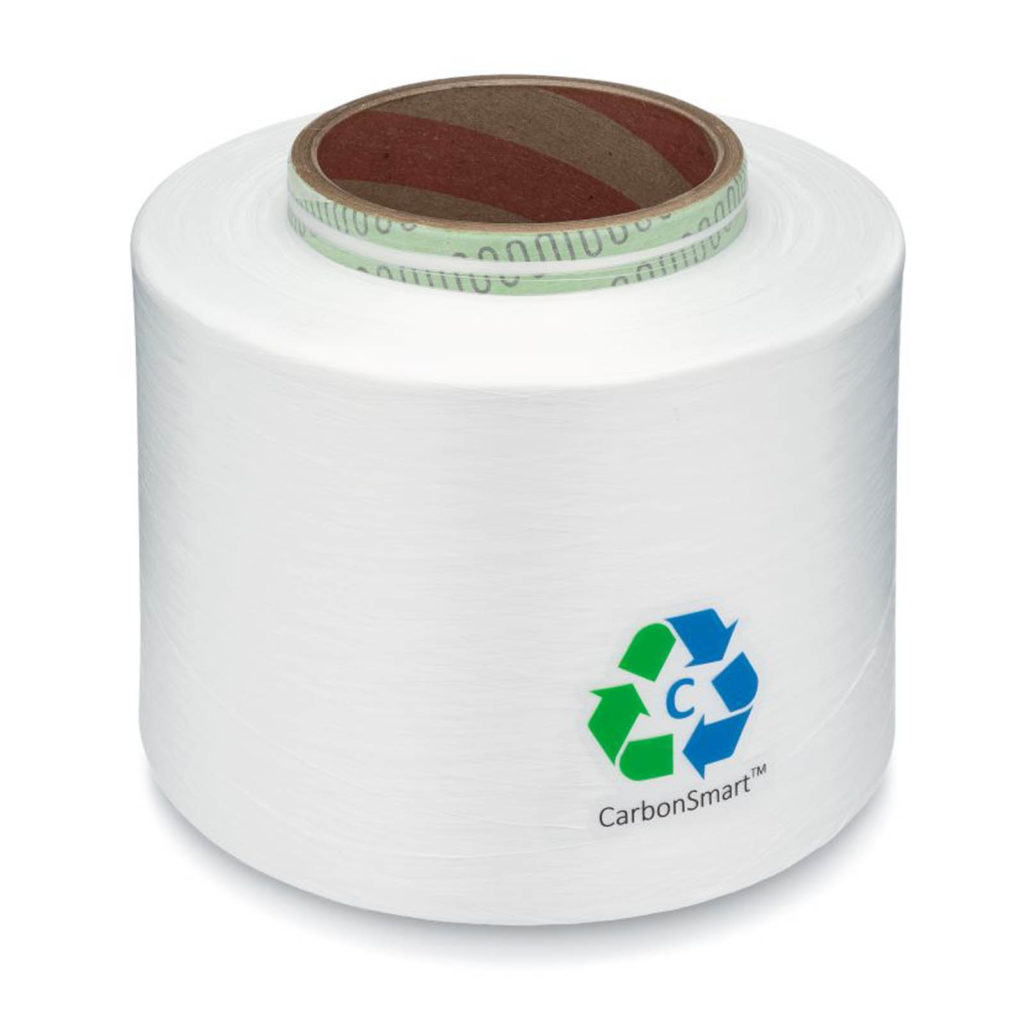
Carbono vem em círculo completo
Por mais impossível que pareça, a mais recente fibra biossintética é criada através da fermentação de resíduos de carbono. A LanzaTech, especialista global em captura de carbono, desenvolveu um processo para criar fibras têxteis (e outros produtos úteis) a partir das emissões de indústrias sujas, como siderurgia, petróleo e produção química – e até mesmo resíduos municipais gaseificados.
A poluição é convertida por bactérias em combustíveis e produtos químicos, como o etanol. A fim de criar poliéster biossintético, o parceiro intermediário India Glycols Ltd. transforma o etanol em MEG, que o Far Eastern New Century (FENC), com sede em Taiwan, usa para fabricar fios de poliéster e têxteis. Embora o poliéster à base de carbono não seja biodegradável, as roupas podem ser recicladas pelo mesmo processo no final da vida útil.
O sucesso do processo LanzaTech foi comprovado em coleções cápsula da marca de vestuário esportivo Lululemon e da varejista global de moda rápida Zara, com tecido de vestuário desenvolvido pela FENC a partir do poliéster biossintético. A empresa chama seu conceito de Carbon Smart.
“Ao reciclar as emissões de carbono, estamos substituindo o carbono do combustível fóssil virgem retirado do solo”, explica Freya Burton, diretora de sustentabilidade da LanzaTech. “Os consumidores agora podem escolher de onde vem o carbono em suas roupas. O conceito é tão novo que estamos todos tentando descobrir como transmitir a mensagem.”
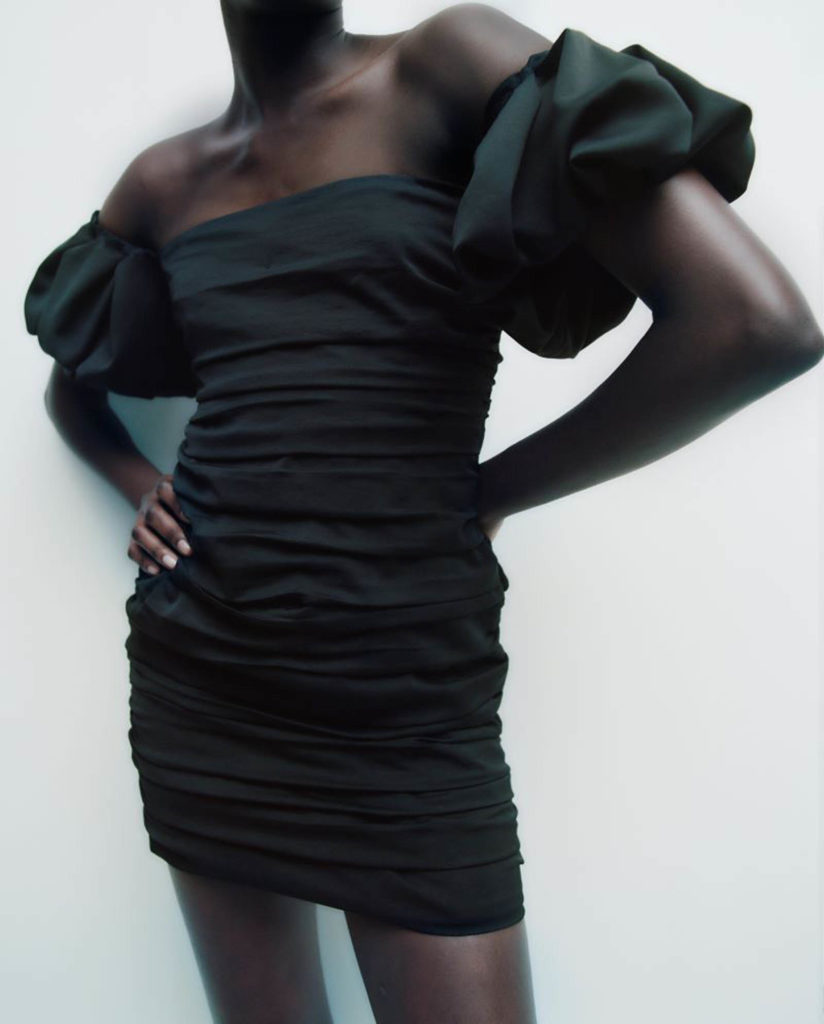
Atualmente, a LanzaTech possui duas fábrica na China e sete fábricas em construção em joint ventures com siderúrgicas. “Há um grande interesse, mais do que podemos acompanhar”, relata Burton.
Embora a LanzaTech tenha licenciado a tecnologia para a criação do etanol, o grande problema é conseguir fábricas suficientes para atender a demanda, diz ela. A empresa também procura usar o processo LanzaTech para criar espuma EVA para calçados e para fabricar fios industriais para transporte e têxteis de interior.
O custo é uma coisa relativa
Embora essas fibras e processos biossintéticos estejam em sua infância, há mais por vir. Sim, serão custosos, pelo menos até atingirem escala de produção; mas esses custos devem ser medidos em relação aos danos ambientais causados pelo uso de sintéticos tradicionais. E as fibras petroquímicas não ficarão baratas para sempre.
A era da abundância para a produção de combustíveis fósseis está morta, impulsionada pelos preços mais altos. Certamente, a atual crise política na Rússia e na Ucrânia terá um efeito negativo sobre a disponibilidade e o preço dos combustíveis fósseis, o que inevitavelmente impactará os produtos têxteis petroquímicos deles derivados.