A tecnologia ActiveMix da Voxel8, startup de Boston, está iniciando a produção de calçados esportivos impressos em 3D em grande escala. Muitas grandes empresas, incluindo Nike, Adidas, Reebok, Carbon e outras, acreditam que o setor de calçados possa ser o primeiro grande adotador de tecnologias de impressão 3D para produção em massa de produtos de consumo. Isso é verdade principalmente para aplicativos de personalização em massa.
Até agora, todas essas empresas se concentraram principalmente na impressão 3D da sola e da entressola. A Voxel8, uma startup com uma história fascinante originária da Universidade de Harvard, está pronta para imprimir o cabedal do calçado, apresentando seu processo ActiveMix exclusivo para extrusão e coloração de materiais avançados de poliuretanos reativos e de alto desempenho. A startup espera permitir que mais empresas ofereçam soluções personalizadas em massa localmente e a um custo menor.
Popularizando a personalização de calçados com impressão 3D
Depois de adquirir experiência em extrusão de materiais múltiplos para o seu pioneiro sistema de impressão 3D em eletrônica, a Voxel8 agora está focada em poliuretanos de nível de engenharia. Esses materiais viscosos são impressos usando o atual sistema ActiveMix da empresa, em uma máquina que a empresa está chamando o ActiveLab.
Nessa abordagem, a cabeça de extrusão usa um complexo sistema de bomba para permitir o controle programável da composição, geometria e propriedades mecânicas dos recursos impressos nas partes superiores (e outros tecidos), bem como em outras formas 3D, como entressolas e solas.
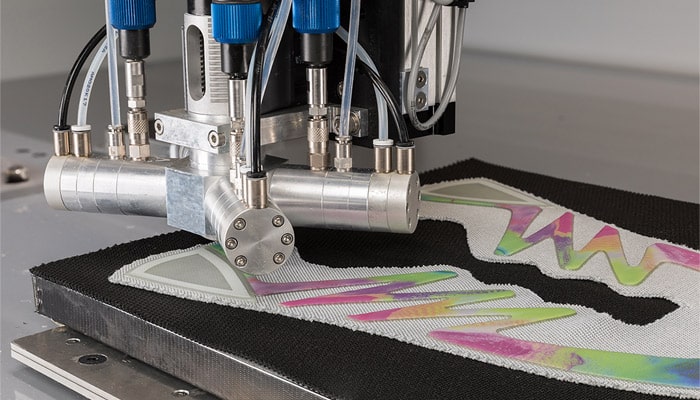
O resultado é que o Voxel8 pode imprimir padrões de poliuretano em 3D em qualquer superfície. Através da integração da tecnologia de jato de tinta, a empresa também pode adicionar imagens e padrões coloridos exclusivos entre as camadas de poliuretano, permitindo maior personalização.
O sistema ActiveLab que agora está disponível no mercado, é adaptado para prototipagem e pequenas tiragens, com coloração, realizadas em uma máquina separada. Mesmo assim, o processo adiciona vários graus de automação a uma abordagem tradicional que exige muita mão-de-obra. Além disso, o próximo sistema de produção ActivePro poderá integrar e automatizar ainda mais os dois processos.
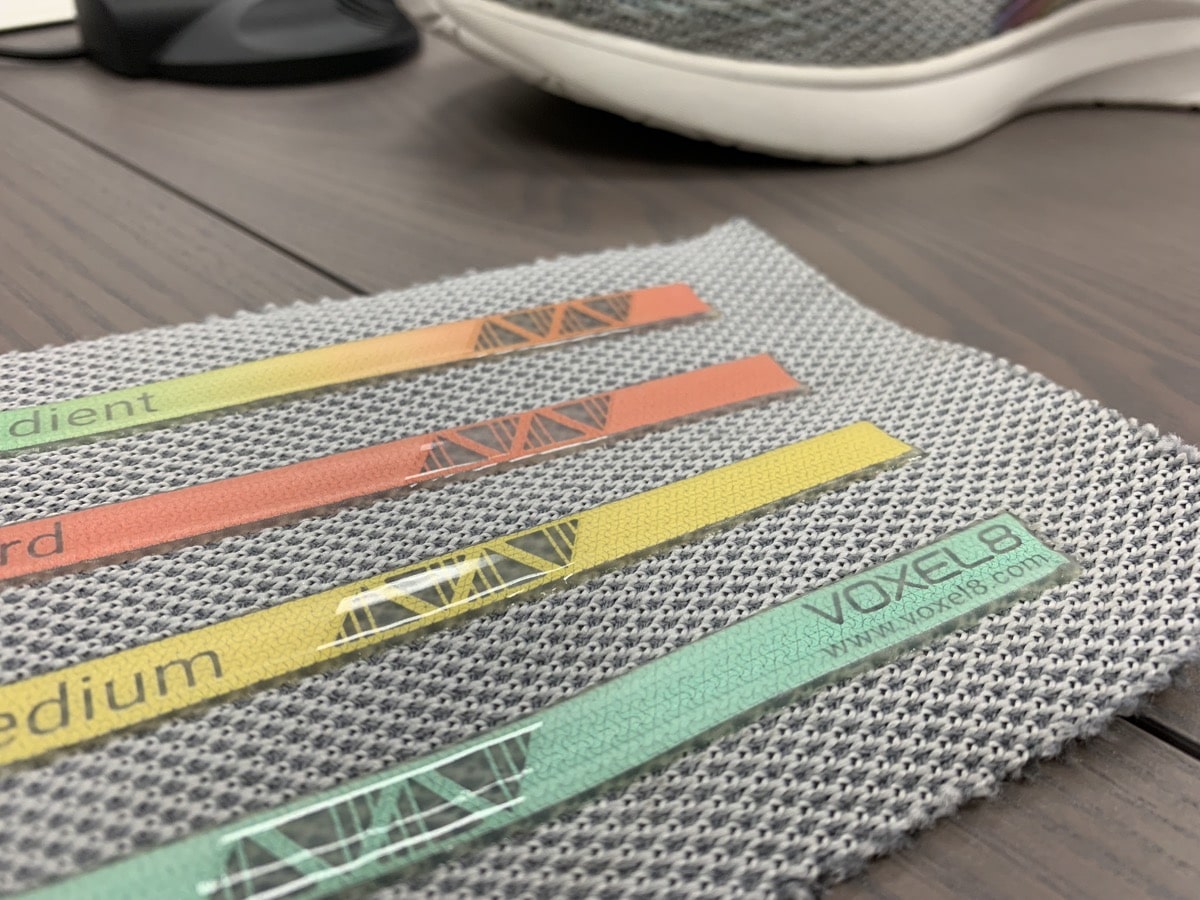
“Nossa visão é abordar uma das áreas de produção de calçados mais intensivas em mão-de-obra, que é a seção superior”, explica os fundadores Travis Busbee e Jack Minardi. “Várias empresas têm se concentrado em entressolas e solados, que são tradicionalmente moldados por injeção. A parte superior é tradicionalmente feita de uma variedade de materiais, incluindo diferentes tipos de tecidos e plásticos com propriedades variadas. Nossa tecnologia permite a personalização em massa das partes superiores através de um processo altamente automatizado que aproxima o design e a manufatura digital do cliente.”
Desatar os laços da fabricação tradicional
Existem duas empresas no mundo que conseguiram comercializar uma impressora 3D eletrônica. Um é Nano Dimension e o outro é Voxel8. O sistema Pro da Nano Dimension permanece focado na eletrônica, enquanto o Voxel8 se aventurou na nova área de sistemas de fabricação de calçados digitais.
Para as duas empresas, os sistemas atualmente disponíveis são destinados a uma etapa intermediária em direção a dispositivos orientados à produção em larga escala. Os sistemas de fabricação digital da Voxel8 visam reduzir drasticamente os ciclos de design e produção, tanto para lançamentos personalizados quanto para, no futuro, execuções de produção em larga escala.
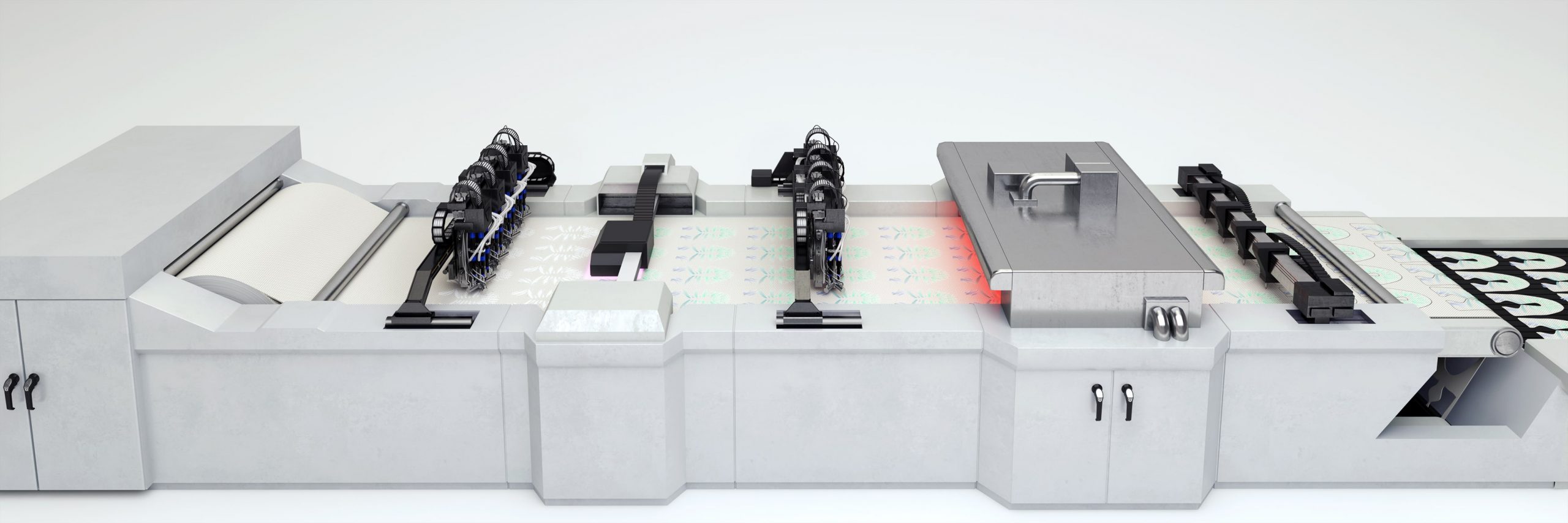
Atualmente, leva de 12 a 18 meses para um designer ter a primeira versão de um novo produto nas prateleiras. Uma das razões é que, enquanto para a maioria das empresas o estágio de design ocorre no Ocidente e a fabricação ocorre na Ásia. O processo de fabricação tradicional requer ferramentas caras e corte de moldes. É muito trabalhoso, com até 100 pares de mãos tocando cada sapato. O que a Voxel8 está fazendo é automatizar o máximo possível disso, começando pela seção superior.
Sapatos Voxel8 totalmente digitais
O sistema de fabricação digital Voxel8 não requer ferramentas, o que resulta em menores custos de instalação e acelera drasticamente o tempo de colocação no mercado. “Podemos criar logotipos, textos e outros recursos estéticos, além de recursos funcionais, como reforços ou contadores de calcanhar com zero ferramentas”, diz Minardi. “Juntamente com a replicação dos processos de fabricação tradicionais a custos mais baixos, também podemos produzir cabedais que atualmente não são fabricáveis.”
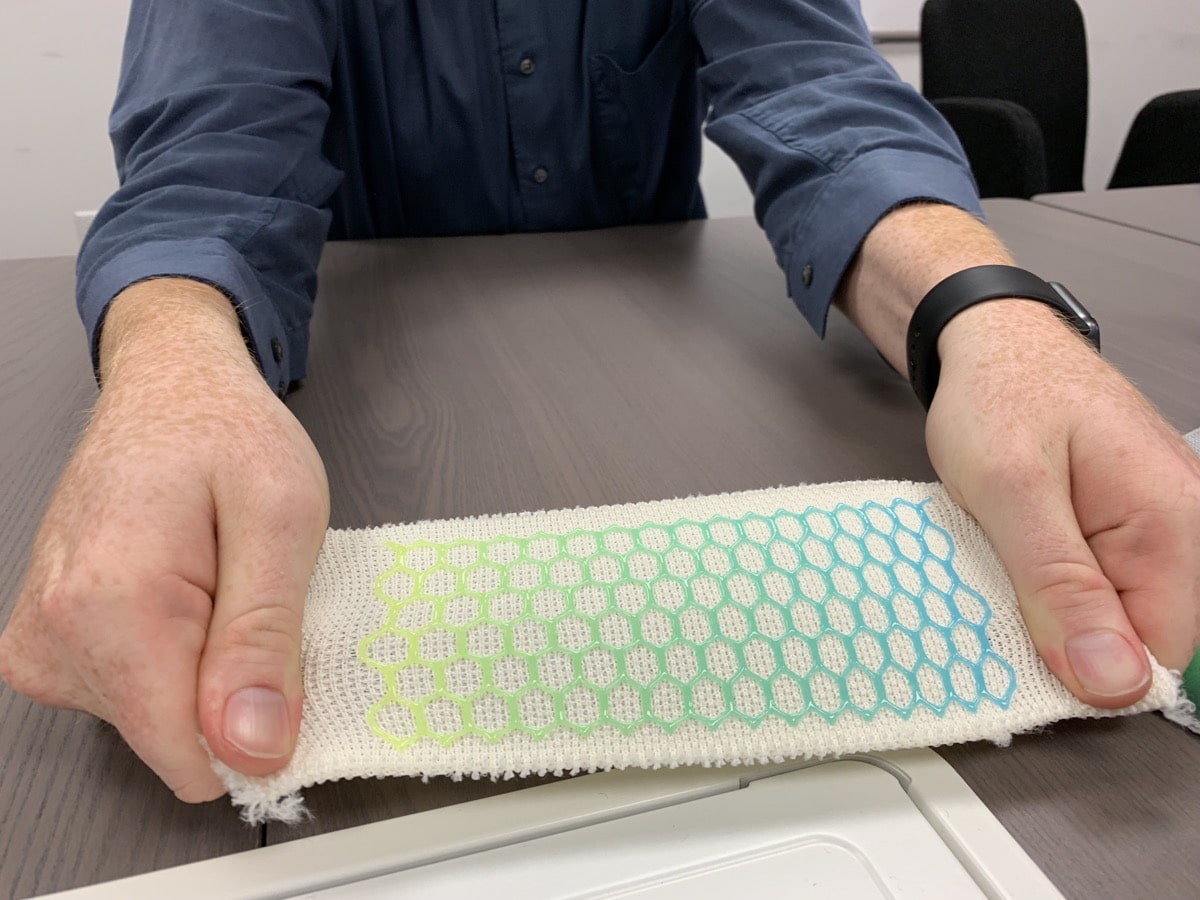
“Por exemplo, podemos variar regionalmente a rigidez e a viscosidade à medida que depositamos o material. Ao regular digitalmente a composição e as propriedades mecânicas de nossos materiais de poliuretano, permitimos que eles forneçam exatamente o suporte que você precisa, exatamente onde você precisa. Além disso, trazemos a cabeça do jato de tinta para cores, entre as camadas transparentes de poliuretano. Isso nos permite utilizar a força, resistência à abrasão e durabilidade dos elastômeros de poliuretano de nível industrial, com a capacidade de cores de alta resolução da tecnologia de jato de tinta” diz Minardi.
Nesta primeira fase, o Voxel8 está chegando ao mercado com o sistema ActiveLab, que integra as formulações dos cabeçotes de impressão, software e materiais proprietários. O sistema atual é econômico em execuções personalizadas de 30 a 50 pares por dia, o que é algo que os fabricantes de calçados estão realmente começando a oferecer. O sistema ActivePro, por outro lado, seria capaz de produzir até 500.000 pares por ano a custos competitivos ou melhores que os processos de fabricação tradicionais da Ásia.
Mini fábrica automatizada de cabedais
Os materiais têxteis vêm em uma variedade de formas, incluindo rolos, malhas planas e malhas de engenharia. O sistema de produção será modular para acomodar tudo isso. Ele terá uma matriz de cabeças de impressão que depositam a primeira camada de poliuretano com propriedades de material ajustadas em zonas, e uma cabeça de jato de tinta aplicará a cor antes que outra matriz de cabeças de extrusão imprima a segunda camada.
A próxima etapa é um forno de cura integrado, que irá curar os materiais em questão de minutos, antes de passar para a etapa final, um cortador a laser, para cortar a forma da parte superior. Tudo o que o operador precisa fazer é carregar o rolo de material têxtil e os componentes de poliuretano. Dentro de alguns minutos, vem uma parte superior completa e personalizada. Além de manter o custo competitivo na produção em massa.
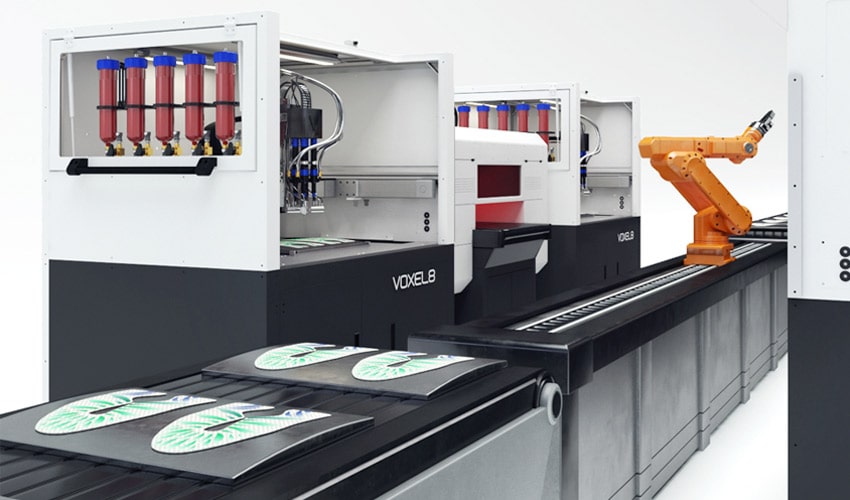
“A melhor parte é que você não pode dizer que é impresso em 3D“, diz Minardi. De fato, o poliuretano sai perfeitamente liso, sem linhas de camada. “Podemos trabalhar com praticamente qualquer tecido superior. Hoje, a parte superior da malha é muito popular, mas nosso sistema nos permite aplicar o poliuretano a praticamente qualquer tipo de tecido e vestuário”.
Pelo menos uma das principais marcas de calçados já fez um pedido do sistema ActiveLab. O sistema ActivePro de grande formato é mais semelhante, em sua aparência externa, às impressoras 2D digitais de grande formato do que uma impressora 3D. Essa abordagem, que implementa a tecnologia de extrusão de material enquanto se concentra no produto final, e não no processo em si, pode ser a chave do sucesso da Voxel8 em finalmente fechar a lacuna entre a impressão 3D e os usuários finais.
Fonte: 3d Printing Media Network